Customization and environmental sustainability make FMV Trasmissioni Meccaniche a key partner in the supply of components and assemblies for power transmission.
Known worldwide for its enchanting landscapes, charming villages, medieval cities, artistic heritage, and last but not least, its food and wine delights, Tuscany is also renowned for the numerous qualified manufacturing companies located throughout the region. Like FMV Trasmissioni Meccaniche, a company founded in 1966, today vertically integrated and well organized into two operational departments: gravity shell casting of aluminum alloys and the complex mechanical workshop where parts and products are fully machined. A lean, flexible, and highly responsive structure that has successfully combined attention to customization with managerial management, also boasting a strong inclination towards innovation and technological upgrading, as well as creativity and expertise.
These qualities are appreciated by industries of all sizes, from small and medium enterprises to large multinationals, operating across various sectors.
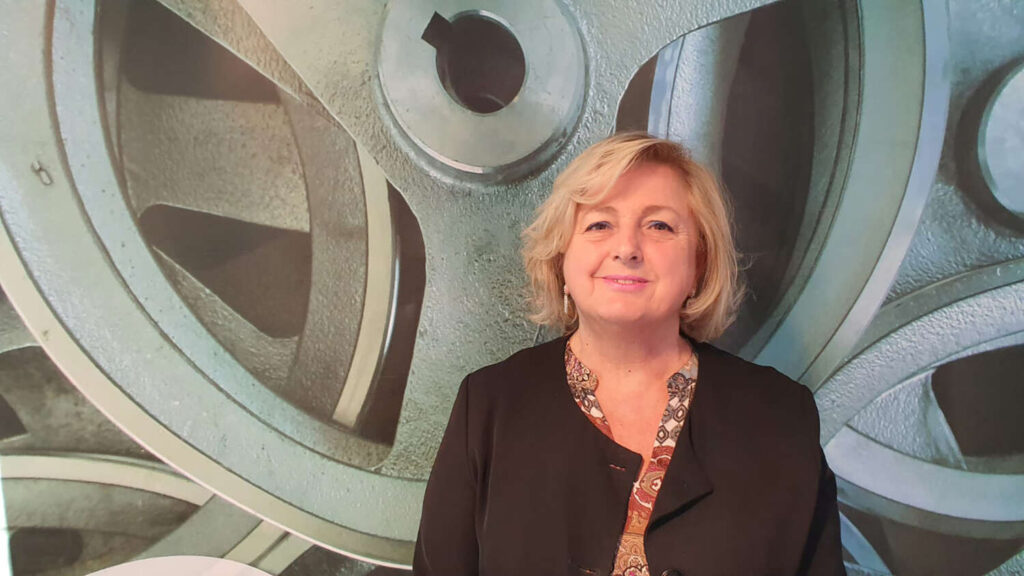
“In over fifty years of activity,” explains Costanza Conti Valiani, owner and president of the company, “we have served manufacturers of food processing machines and plants, construction machinery and agricultural equipment manufacturers, as well as electric motors, pumps, compressors, just to name a few fields.
For some of them, for quite some time now, our support has extended from traditional subcontracting to the role of project leader, with the ability to deliver assemblies, such as those made for power transmission, assembled internally and complete with our components and all necessary parts.”
High-Productivity Process Technologies
FMV Trasmissioni Meccaniche operates at its headquarters in Poggibonsi, on a covered production area of over 2,000 sqm, supported by a cohesive and growing team of collaborators, aided by state-of-the-art technologies and a constantly updated machine park. More specifically, regarding the foundry department with gravity shell casting of aluminum alloys (with the capability to handle over 10 different alloys), the company has 18 shell molders and several melting furnaces.
“In the department,” explains Lisa Valiani, R&D Engineer and Coordinator at FMV Trasmissioni Meccaniche, “a new high-performance robotic cell is being introduced, which significantly increases both the quality and variety of production, allowing for the handling of heavier alloys and castings than before.”
Examples of products that have benefited from these improvements are targeted at the compressors and pumps markets.
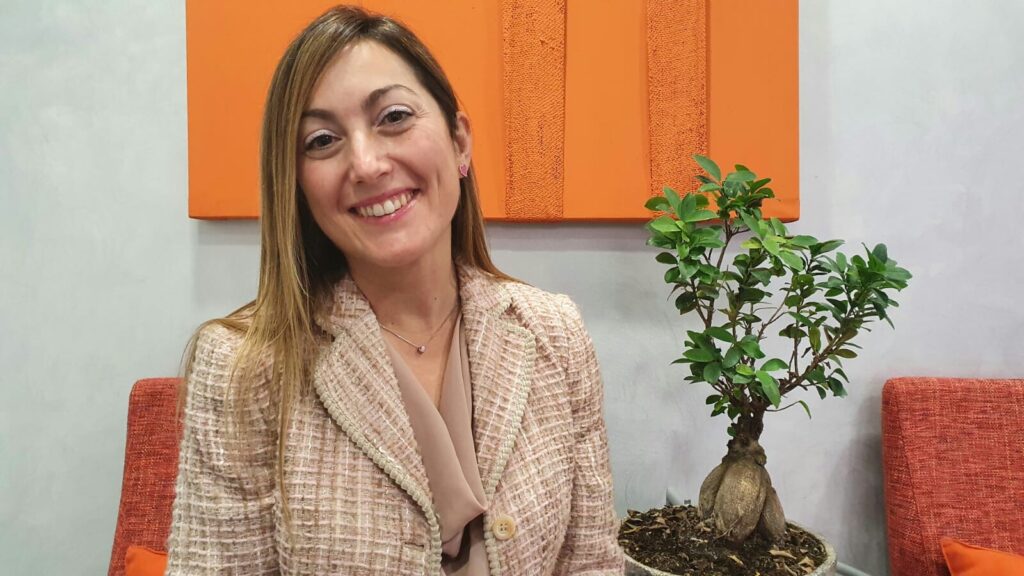
“To this robotic cell that handles the casting of the material,” adds Eng. Valiani, “we have added two new melting furnaces and updated the machine software for optimized control. Essentially, we have combined foundry production capacity with a higher level of quality.”
Equally well-equipped technologically is the mechanical workshop, which houses three machining centers complete with pallet changers, numerous lathes (some of which are robotic and equipped with automatic loaders), a bar lathe, as well as a grinding machine, threaders, slotters, broaching machines, and a marking machine.
Certified Quality and Environment for an Integrated Management System
“The new robotized cell in the foundry,” adds Costanza Conti Valiani, “together with one of the aforementioned machining centers with pallet changers installed in the mechanical workshop, are part of the Industry 4.0 investments planned over the last two years. These new integrations perfectly reflect our ongoing pursuit of process optimization to achieve the highest quality levels of the components and assemblies requested by our customers.”
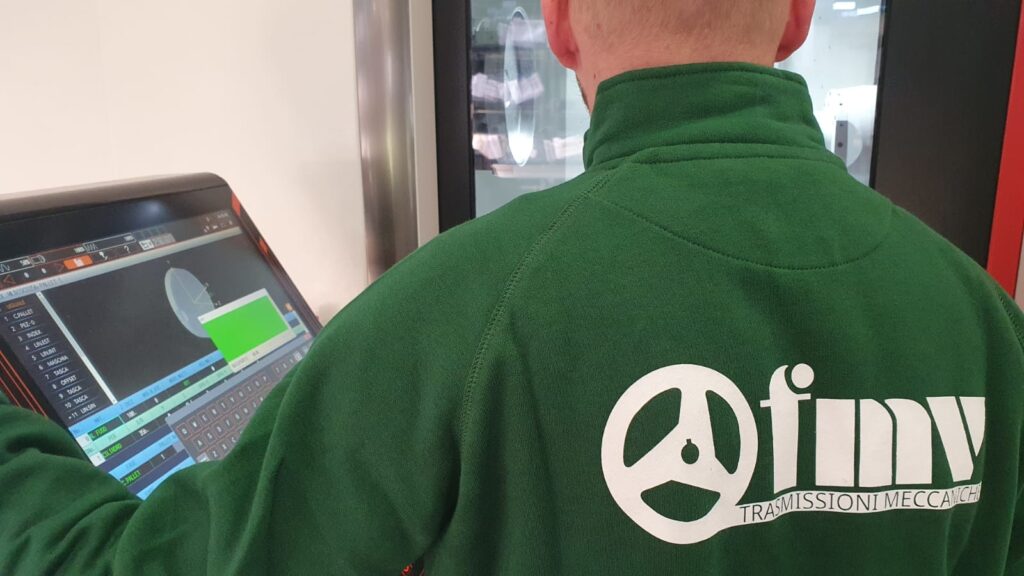
Quality is guaranteed and certified not only on the machine or in-process, but also by the presence of a metrology room set up within the mechanical workshop and a radioscopic machine, where all critical dimension inspections requested by customers are carried out. It is worth noting that FMV Trasmissioni Meccaniche considers quality and environmental protection fundamental elements of its business strategy. To this end, the company applies an Integrated Management System (quality and environment) compliant with UNI EN ISO 9001 and UNI EN ISO 14001 standards. The integrated management system is based on the strong convictions of Management regarding the satisfaction of all customer needs, both external and internal, a deep sensitivity towards the surrounding environment and related issues, and the integration requirements stemming from the reality and local community in which the company operates and is embedded.
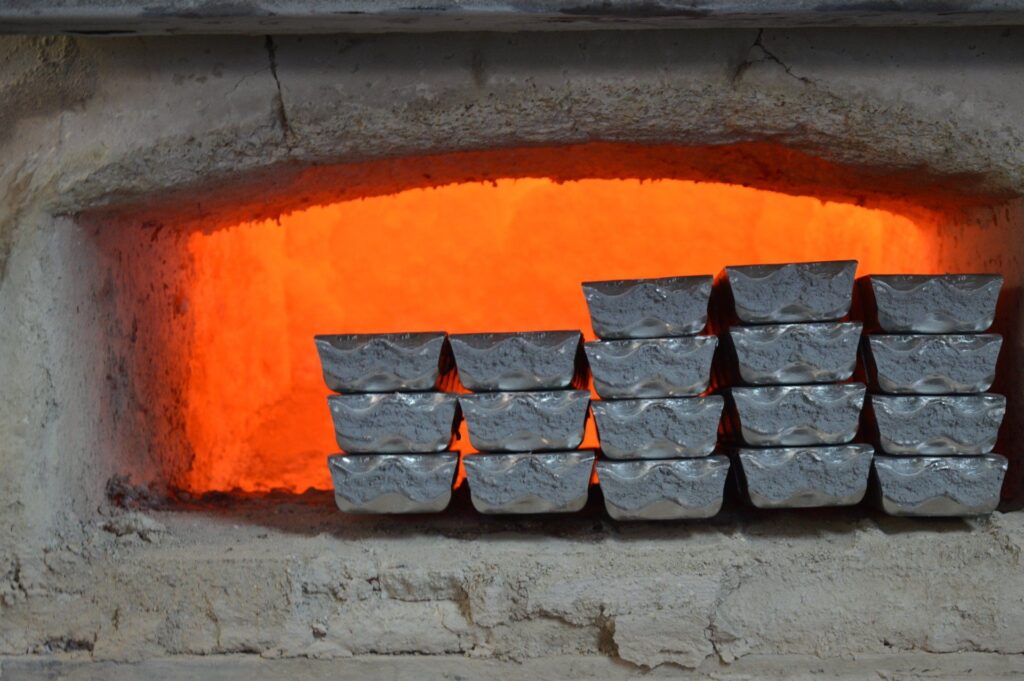
“Environmental sustainability,” emphasizes Eng. Lisa Valiani, “is an integral part of our daily activities and beyond. We have created a new work platform focused on ‘re-use’ within the circular economy and are working on new development projects.”
A key factor in achieving these results is also the internal technical office, headed by Sergio Valiani, husband of the owner and president Costanza Conti Valiani, who oversees and directs the entire foundry and mechanical workshop departments, together with a mechanical engineer and his son Emilio Valiani, who is directly involved in production line management and all CAD/CAM operations.
The Keys to Success for Continued Growth
Founded as a foundry in the 1960s, FMV Trasmissioni Meccaniche has successfully adapted to new market dynamics by progressively expanding its services, starting the production of pulleys, as well as much more complex types of castings, always using gravity shell casting.
“One of our strengths,” notes Costanza Conti Valiani, “is definitely our ability to produce large-sized components and to study and find the best solutions for our clients. We manufacture over 2,000 types of components annually with a high introduction rate of new components each year. It is certainly a point of pride to be able to internally design and solve complex problems, thanks to being a vertically integrated company managing processes from material casting, machining, through to inspection and final assembly.”
The production of this Tuscan company is directed approximately 35% abroad, with a direct presence in the markets of France, Spain, the Netherlands, Belgium, the United Kingdom, Ireland, Sweden, Romania, as well as in South Africa and Turkey.
“Indirectly,” confirms Costanza Conti Valiani, “thanks to the multinational companies that are our clients, the mechanical components we produce are well distributed across all continents, as well as in various sectors previously mentioned. In short, a made-in-Italy product and, even more so, a made-in-Tuscany product with a global reach.”
Thanks to this market and sector diversification, the company has consistently managed to increase its turnover, even during difficult periods such as those experienced in recent years, including the pandemic and an often unstable global context. Driving this growth has always been the entrepreneurial foresight of the owners, supported by the third generation present in the company, capable of combining technology and high customization into a winning mix. An evolution that has also seen FMV Trasmissioni Meccaniche take a leading role in the digital transition that began in 2020.
Industry 4.0 to Overcome New Market Challenges
With most of its plants interconnected according to the requirements of Industry 4.0, FMV Trasmissioni Meccaniche looks to the future with significant growth ambitions.
“In addition to completing this digital transition,” clarifies Costanza Conti Valiani, “having already implemented software linked to production planning and industrial accounting allows us to constantly communicate with the machines themselves and evaluate all key performance indicators. This helps to rationalize and optimize order management, with a view to greater competitiveness and to better serve the market and our customers.”
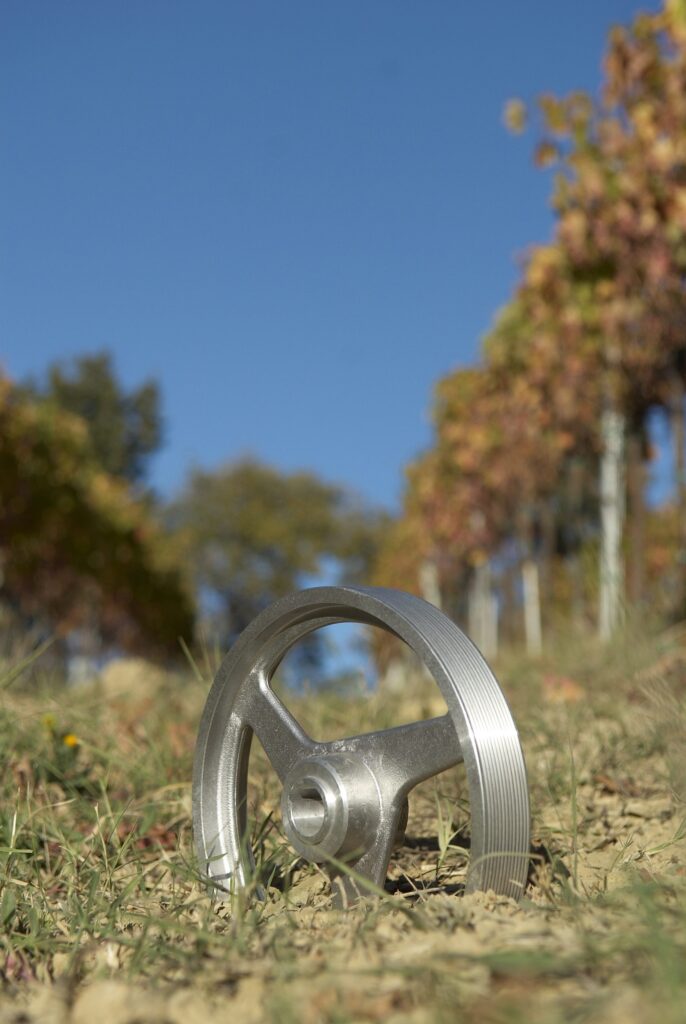
Industry 4.0 and Technological Innovation to Overcome New Market Challenges, and More.
“Given the positive growth expectations,” concludes Costanza Conti Valiani, “among future projects is also the consideration of establishing a new production site. We actually have an additional 6,500 square meters of land, besides the existing 2,000 already built on, a space intended for creating a new production unit. The idea is to keep the foundry at the current historic location, while relocating the mechanical workshop and all related activities to the new area.”
A new unit, which remains closely tied to the territory — always an integral and distinctive part of FMV Trasmissioni Meccaniche of yesterday, today, and tomorrow.
(by Gianandrea Mazzola)
Source: Meccanica News